Because digital twins make operations healthier and more effective, they have the potential to transform conventional mining methods completely.
So, here are some of the benefits of digital twin mining.
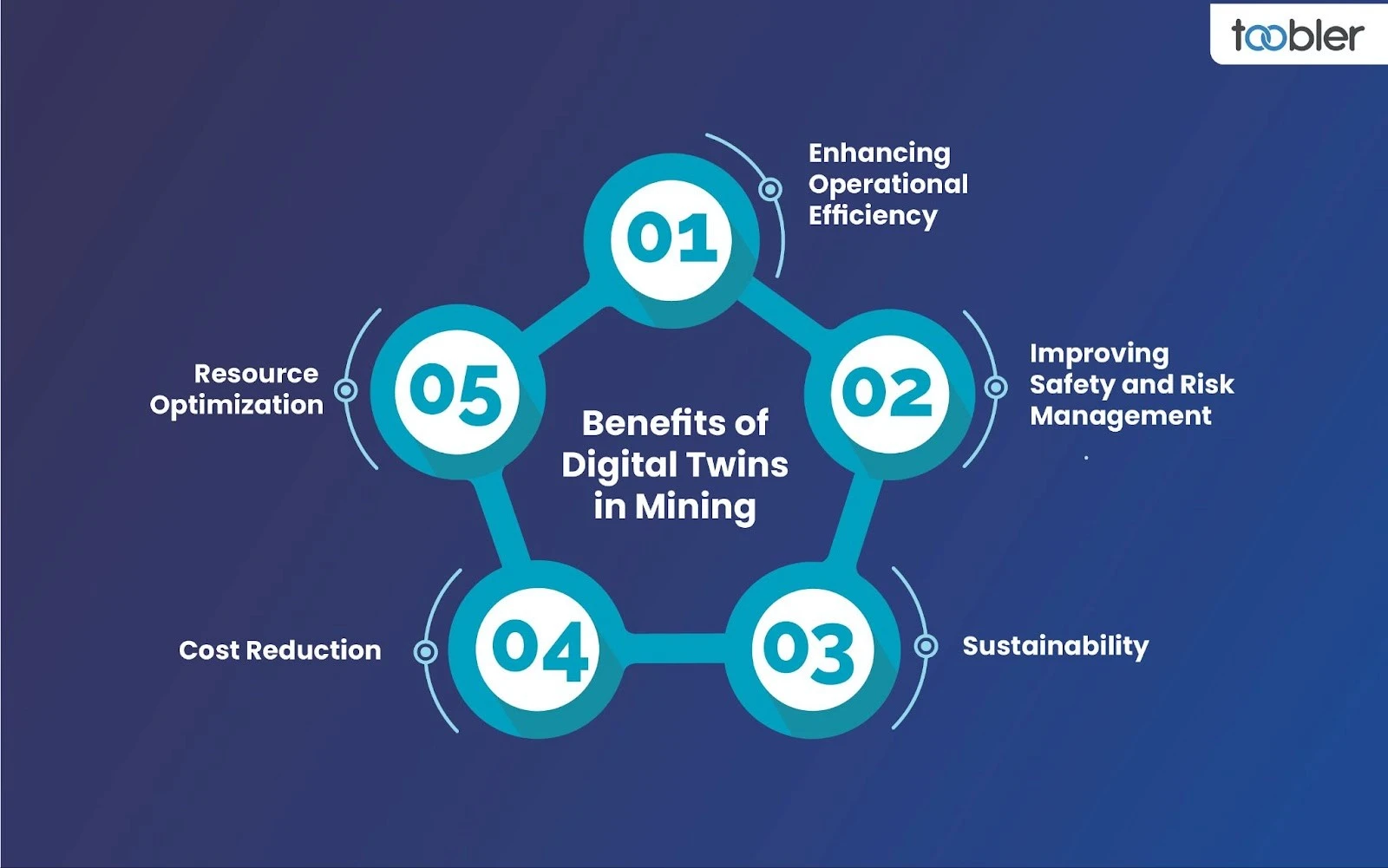
1. Enhancing Operational Efficiency
Consider having an online assistant watch over every facet of your mining business at all times. Digital twins make that contribution.
Digital twins allow monitoring and analyzing data in real time by generating a digital duplicate of physical assets, systems, and processes. Mining businesses can use this ability to ensure that everything is operating smoothly, discover inefficiencies, and streamline procedures.
For example, digital twins are able to forecast when an equipment component is going to break, which enables prompt repair and prevents costly interruptions. In addition to extending the life of the equipment, predictive maintenance helps to guarantee that activities run smoothly and without disruption.
Digital twins, in short, enable mining businesses to work more productively while conserving resources and time.
2. Improving Safety and Risk Management
Because the mining workplace is by nature unsafe, safety is of the utmost importance. Digital twins offer comprehensive insights into operational circumstances, greatly improving safety and risk management. By modeling different scenarios, digital twins can anticipate potential risks and recommend preventive actions.
Digital twins, for instance, can analyze geological information to identify spots of instability in a mine. With this information, businesses can ensure employee safety by proactively reinforcing certain areas.
Moreover, response groups can receive real-time data from digital twins in a critical situation, which enables them to act swiftly and decisively. This preventive approach to security has the potential of avoiding fatalities and saving lives.
3. Sustainability
Digital twins present a feasible solution to the mining sector’s increasing urgency to reduce its negative ecological impact. By maximizing resource utilization and decreasing waste, digital twins help promote more environmentally friendly mining methods.
Digital twins can assist businesses in selecting the most environmentally friendly solutions by simulating the ecological impacts of various mining methods. They may, for instance, track emissions and resource usage in real-time, allowing businesses to make changes that lessen their environmental impact. This ability is essential for mining businesses trying to boost their sustainable reputation and comply with regulations.
Please read our blog on Digital twins and sustainability to understand how digital twins help in the sustainable development of products or services.
4. Cost Reduction
Lowering operating costs is one of the most appealing advantages of digital twins. Digital twins save mining companies money by streamlining procedures and eliminating errors.
Digital twins, for instance, can improve drilling performance and cut down on resource and labor waste. Mineral extraction becomes more effective, increasing productivity while lowering expenses because of its accuracy.
Furthermore, digital twins’ predictive maintenance ability is associated with fewer expensive replacements and delays. Thus, digital twins dramatically reduce costs by maintaining streamlined and successful processes.
5. Resource Optimization
Resource optimization is essential in a sector where equipment and supplies are costly and frequently in short supply. Businesses may make the most of their resources by using digital twins, which offer comprehensive information on resource use.
Digital twins, for instance, can monitor raw materials, energy, and water usage to pinpoint locations where resources are being misused. Businesses can then implement plans to save waste and boost productivity, promoting sustainable behaviors while simultaneously increasing profits.
Digital twins in mining enable businesses to meet their operational objectives more sustainably by guaranteeing that resources are used as efficiently as feasible.
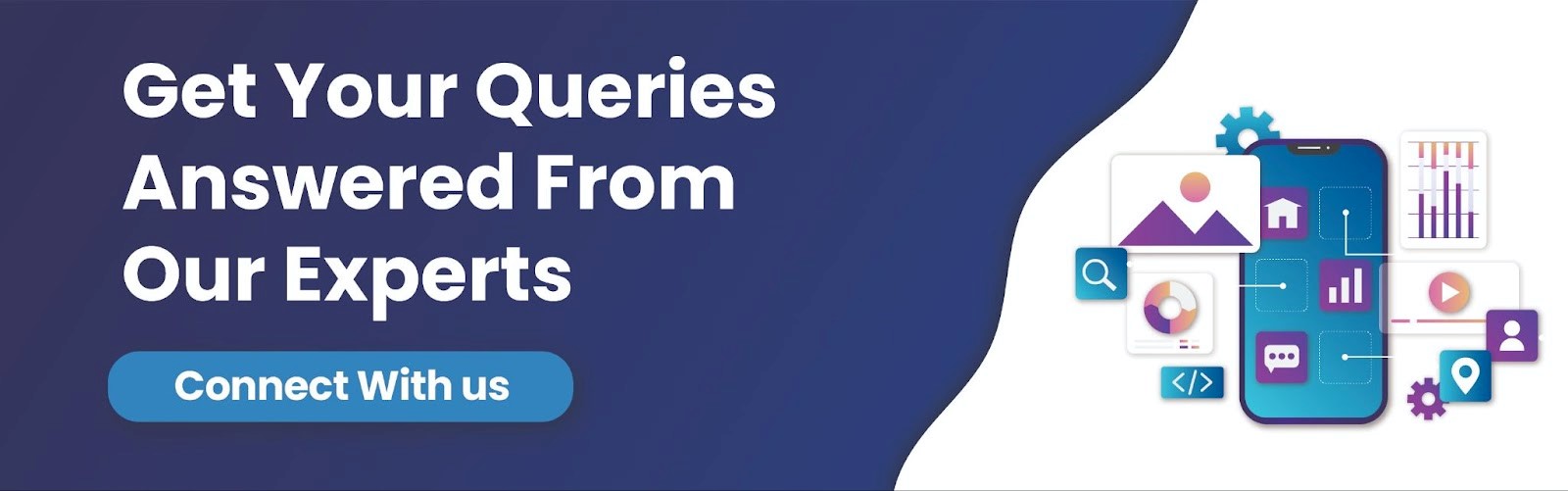